Bar-Type LCDs: The Engineer’s Guide to Maximizing Information in Constrained Spaces
The Pain Point: When Standard Displays Just Won’t Fit
In the world of industrial design and commercial systems, space is a premium commodity. Engineers and product managers constantly face the challenge of integrating clear, functional displays into equipment with non-standard form factors. Standard 4:3 or 16:9 LCD panels, while ubiquitous, are often too wide or too tall for applications like 1U rackmount servers, narrow equipment control panels, public transportation information systems, or dynamic retail shelf edges. This forces a compromise: use a smaller, less effective display, clutter the interface with an array of simple LEDs and seven-segment displays, or accept a bulky design that wastes precious real estate. This is not just an aesthetic issue; it’s a functional one that can impact usability, efficiency, and the user experience.
The core problem is that information needs are growing, but physical space is not. A technician needs to see detailed diagnostics at a glance on a server front panel. A commuter needs clear, scrolling updates on a narrow overhead display in a train car. A shopper benefits from dynamic pricing and promotions displayed directly on the shelf edge. In each case, a traditional display is the wrong tool for the job. This is the engineering challenge that bar-type, or “stretched,” LCDs are specifically designed to solve.
What Are Bar-Type (Stretched) LCDs and How Are They Made?
At first glance, a bar-type LCD might seem like a completely new display technology. In reality, it’s an ingenious and highly precise modification of standard TFT-LCD technology. Instead of being manufactured from scratch in their unusual aspect ratios, stretched displays are typically created by cutting a larger, standard-format panel (e.g., a 32:9 panel might be cut from a 16:9 panel). This process allows for a wide variety of “ultra-wide” aspect ratios that would otherwise be economically unviable to produce as a native size.
The Manufacturing Process: Precision Cutting and Sealing
Creating a reliable, industrial-grade bar-type display is a multi-step process that demands extreme precision. It’s far more complex than simply taking a saw to a standard screen.
- Mother Glass Selection: The process begins with a large, high-quality “mother glass” panel. The final dimensions and resolutions of the bar-type displays depend on the properties of this original panel.
- Glass Scribing and Breaking: The panel, which consists of a TFT glass substrate, a color filter substrate, and the liquid crystal sealed between them, is placed in a precision cutting machine. A diamond or laser scriber creates a microscopic score line on the glass. Then, a controlled mechanical force is applied to create a clean break along this line.
- Edge Resealing and Circuitry Rerouting: This is the most critical and proprietary step. Once cut, the edge of the display is exposed, leaving the liquid crystal vulnerable to leakage and contamination. A specialized sealant is meticulously applied to the new edge to create a perfect, durable seal. Furthermore, the cutting process severs some of the original gate and source driver connections. The manufacturer must re-route these electronic pathways on the remaining panel area to ensure that every pixel on the new, smaller display is still addressable by the control board. This is a highly technical feat that separates high-quality displays from unreliable alternatives.
- Backlight Customization: The original backlight unit is either cut and reconfigured or, more commonly, a completely new, custom-designed LED backlight strip is created to match the new form factor, ensuring uniform brightness across the entire stretched surface.
This process transforms a standard panel into a specialized component, ready for integration into space-constrained designs. When sourcing these displays, it is crucial to partner with suppliers like SLW-ELE, who provide high-quality panels like the G156HTN02-0, ensuring that this manufacturing process is done to the highest industrial standards. For a deeper understanding of the underlying technology, our guide on The Ultimate Guide to TFT LCD is an excellent resource.
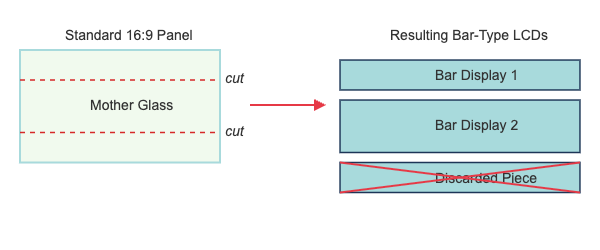
Key Technical Specifications: What to Look for in an Industrial Bar-Type Display
Selecting the right bar-type LCD involves looking beyond the unique shape. The underlying specifications are critical for ensuring performance and reliability in demanding environments. Engineers should scrutinize the datasheet for the following parameters.
Parameter | Why It Matters for Bar-Type Displays | Recommended Specification for Industrial Use |
---|---|---|
Aspect Ratio & Resolution | The non-standard ratio (e.g., 16:4.5, 32:9) is the key feature. Resolution must be sufficient to display content clearly without pixelation, especially for text. | Choose based on the application. For shelf edges, a lower vertical resolution may be fine. For control panels, higher pixel density (PPI) is needed for sharp graphics. |
Brightness (cd/m² or Nits) | Many bar displays are used in high ambient light environments (retail stores, outdoor kiosks, vehicle cabs). High brightness is essential for readability. | 450-700 nits for indoor use. 1000+ nits for sunlight-readable or outdoor applications. |
Viewing Angle | These displays are often viewed from off-center angles (e.g., looking up at a transit display, looking down at a rackmount server). A wide viewing angle prevents color and contrast distortion. | Minimum 170°/170° (Horizontal/Vertical). IPS or MVA technology is highly preferred over standard TN panels. |
Operating Temperature | Industrial and transportation applications often involve extreme temperatures. The display must function reliably without failure. | -20°C to +70°C is a common industrial range. Wider ranges (-30°C to +85°C) are available for more demanding environments. |
Durability & Sealing | The cut edge is a potential failure point. The quality of the seal determines the display’s long-term resistance to humidity, dust, and vibration. | Look for manufacturers who detail their sealing process. Conformal coating on the driver board PCBA is a plus for harsh environments. |
Application Deep Dive: Where Bar-Type LCDs Create Value
The true impact of bar-type displays is best understood through real-world applications where they solve specific, costly problems.
Case Study 1: The Smart Retail Shelf Edge
- Problem: A large grocery chain was struggling with the high labor costs and inaccuracies associated with paper price labels. Updating prices for a single weekly promotion required hundreds of man-hours across their stores, and pricing errors led to customer dissatisfaction and lost revenue.
- Solution: The chain retrofitted their key aisles with 23.1-inch shelf-edge bar displays from a reputable manufacturer like AUO. The displays were networked to the central pricing server, allowing for instant, store-wide updates. They could now display not just the price, but also promotions, nutritional information, and even short video advertisements.
- Result: Labor costs for price changes were reduced by over 90%. Pricing accuracy reached 99.9%. Furthermore, in-store testing showed a 5% average sales uplift for products featured on the dynamic displays, thanks to their eye-catching nature.
Case Study 2: Industrial Control Panels & 1U Rackmounts
- Problem: A manufacturer of network security appliances used 1U rackmount chassis. The front panel was limited to a few status LEDs and a basic two-line character LCD. When a device had an issue, technicians had to connect a laptop and run diagnostic software to understand the problem, increasing downtime.
- Solution: They integrated a 7-inch ultra-wide bar-type display with a resolution of 1280×240 into their new product design. The display provided a rich graphical interface showing real-time network throughput, CPU/memory load, internal temperatures, and detailed, human-readable alert messages.
- Result: On-site diagnostic time was reduced by an average of 40%. “At-a-glance” monitoring became possible, allowing data center staff to spot anomalies proactively before they became critical failures. The modern look also significantly enhanced the product’s perceived value. A similar approach can be taken with panels such as the G121XCE-L01, which can be sourced for custom cutting.
Overcoming Integration Challenges: A Practical Checklist for Engineers
Integrating a non-standard component like a bar-type display requires careful planning. Here is a checklist to guide the process:
- Mechanical Fit & Mounting: The elongated form factor is more susceptible to torsion and vibration. Ensure your product’s chassis provides adequate support along the length of the display. Custom bezels are almost always required.
- Driver Board & Connectivity: Verify that the display’s controller board (AD board) supports the native, non-standard resolution. Standard controllers may not work. The interface, typically LVDS or eDP, must be compatible with your host system’s video output.
- Thermal Management: A long, thin backlight can concentrate heat. Ensure there is adequate airflow or a heat-sinking path away from the back of the display, especially for high-brightness models operating in warm environments.
- Content Design: This is a critical software/UI consideration. Your graphical assets and text must be designed specifically for the ultra-wide aspect ratio to avoid stretching, distortion, or cropping. Work closely with your UI/UX team.
- Power Supply: Ensure your power rails can supply the necessary voltage and current, particularly for the high-power backlights found in sunlight-readable models.
The Future is Unconventional: Trends in Custom-Shaped Displays
Bar-type displays are just the beginning. The same core technology of cutting mother glass is paving the way for even more unconventional shapes. We are seeing a rise in demand for circular displays for smart home devices and gauges, square displays for compact IoT products, and even panels with custom corner cut-outs to fit perfectly around other components. Display manufacturers like Tianma are leaders in this space. As manufacturing techniques for both LCD and OLED panels continue to advance, the rigid rectangle will no longer be a design constraint, allowing for truly seamless and organic integration of displays into products of all shapes and sizes.
Conclusion: More Than Just a Cut-Down Screen
Bar-type LCDs are far more than a novelty. They represent a mature, reliable, and powerful solution to a pervasive engineering problem: the need to display rich information in physically constrained spaces. By understanding the manufacturing process, selecting for key industrial specifications, and planning integration carefully, engineers can leverage these displays to create more efficient, user-friendly, and modern-looking products. They unlock design possibilities in transportation, retail, industrial automation, and medical devices that were previously impossible with standard-format screens.
For your next project facing spatial constraints, don’t compromise on the user interface. Consider the strategic advantage of a bar-type display. Explore our range of industrial LCD solutions or contact our engineering team to discuss your specific custom-cut requirements and find the perfect fit for your application.